Greater level of capacity and a better product quality
If Gebr. Kramer, a fish processing company in Urk, would like to renovate the entire deep-freeze department, Equans is facing a major challenge. “With the limited space available, it is a case of fitting things in and carrying out measurements”, explains co-owner Lub Kramer. As soon as the final plan is on the table, Equans will complete the task in record time. And Kramer will benefit from a greater level of capacity and a better product quality.
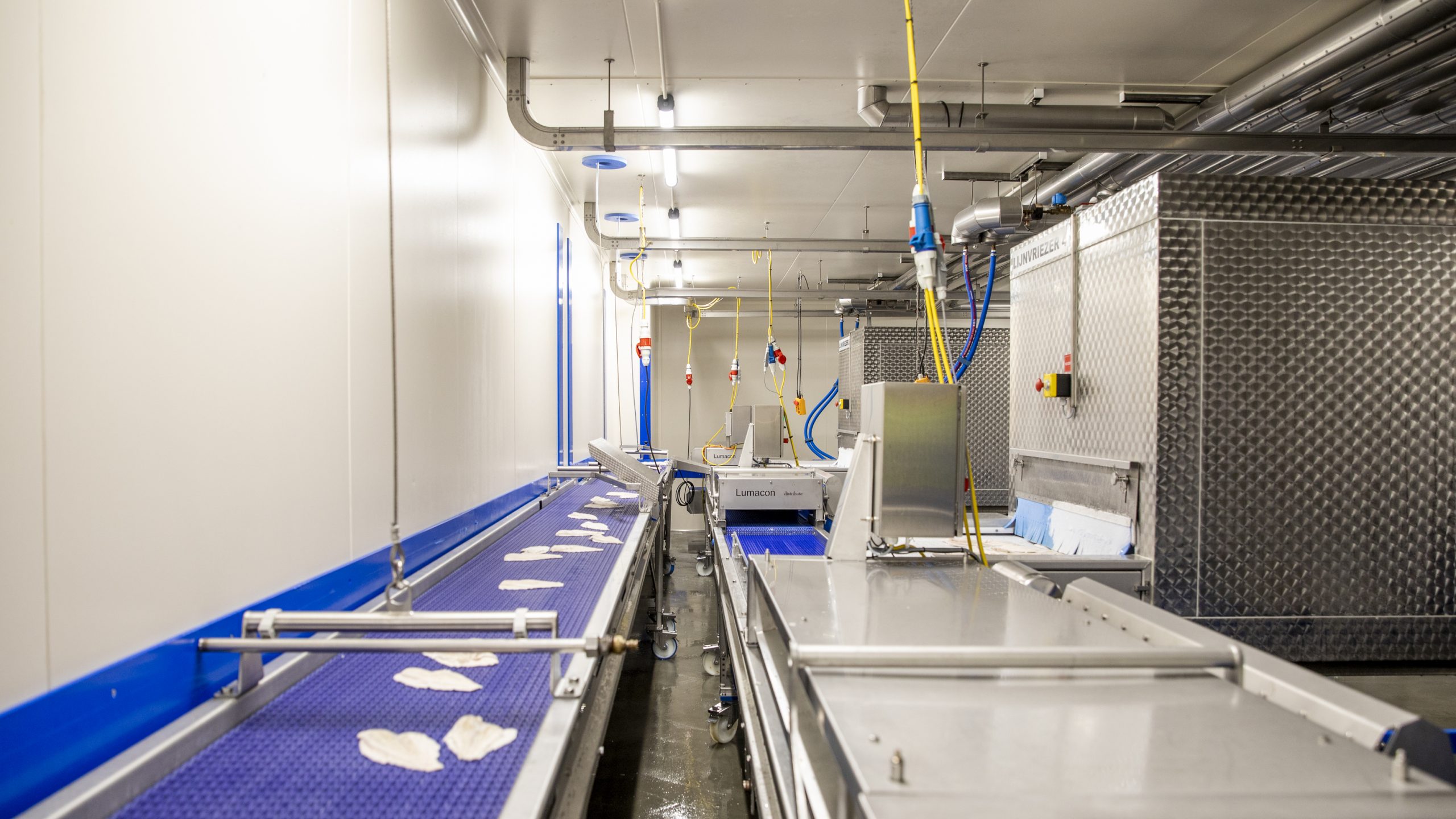
Equans’s design for the new freezer installation will increase capacity. This is something that appeals to brothers Lub and Klaas Kramer, but several procedures are still needed in order for this to become a reality. From removing the loft to relocating the refrigerating system, that runs on natural refrigerants, is no longer located within the building, but on the roof. This is safe and, of course, equipped with a soundproof and fire-resistant prefab casing. As a result, more space is created for the deep-freeze tunnel in the depot.
Project Manager Chris Muller of Equans has another trick up his sleeve for increasing the capacity. He is replacing the only belt freezer with a 2.60-metre air injection freezer (ILV) with two 1.80-metre deep-freeze belts. “The dual deep-freeze line allows Gebr. Kramer to process larger amounts of plaice and sole in a shorter time; around 1,300 to 2,000 kilos per hour. The second line also provides a back-up that is immediately ready in the event of a possible malfunction”, explains Muller. A fillet of plaice is frozen at a temperature of -40°C. Instead of taking 20 minutes, this now only takes 5 minutes at most. This more rapid freezing results in excellent savings, as the energy consumption needed to freeze 1 kilo of fish is halved.
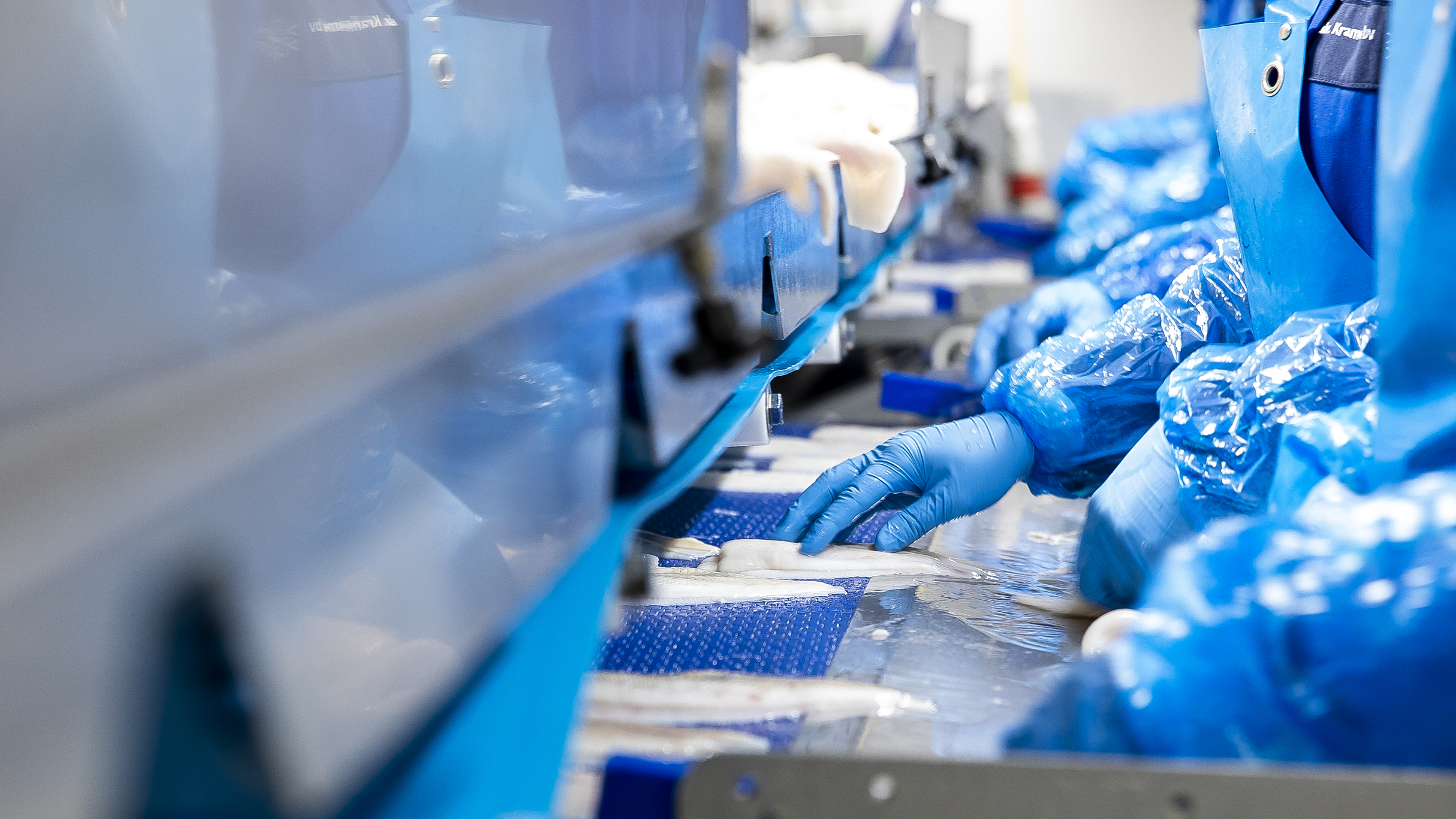
The fish itself also thrives better with the faster deep-freeze time. Deep-freeze specialist Juriaan Romkes shares his experience: “I can already see the difference as soon as the fish come out of the ILV. The fish are lighter and whiter. And an imprint can barely be seen thanks to the fine structure of the transport conveyor. The fish even look good on the inside: the structure remains unspoiled because the ILV does not extract as much fluid. This means that the fish do not dry out as much and maintain their weight better.”
The Kramer brothers are reaping the benefits of this as entrepreneurs. “The ILV has a longer standing time as it extracts less fluid and thus is less affected by the accumulation of ice. But the most important thing of all is customer confidence. Since the new freezer installation was commissioned, our fish are better and we are much busier”, explained Kramer.
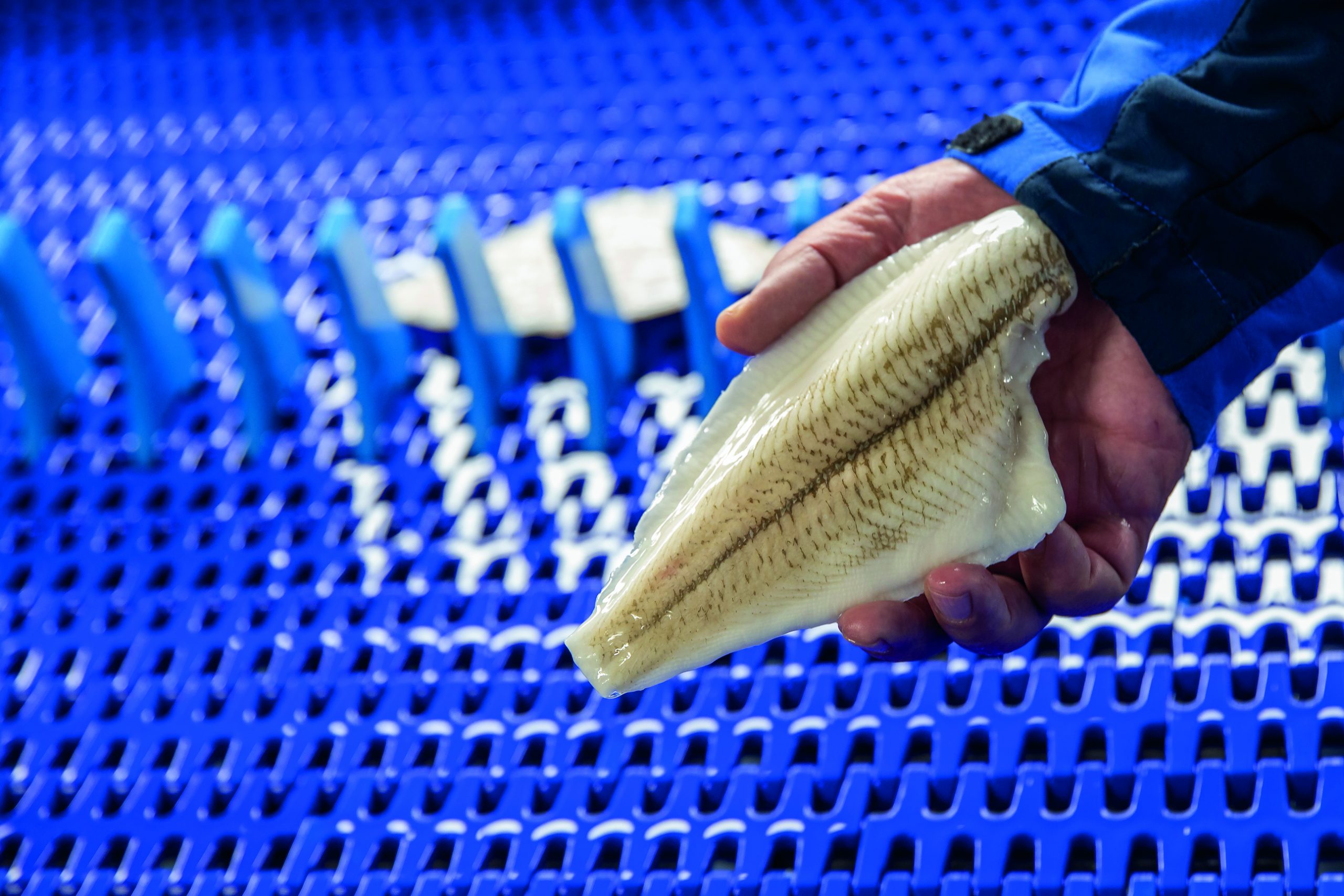
After treatment in the ILV, the post-freezing phase ensues. Where the fish originally went through two line freezers, they now go through five tunnels along their route. The fish are hardened further here at a temperature of -38°C. An ice cold plunge in a pool of 0°C water follows after every line freezer, allowing the fish to absorb up 10 to 50% ice. Thanks to this fine layer of ice, the fish is protected against drying out and freezer burn and ultimately has a longer shelf life.
As the new glazing containers are smaller in size and more shallow, a quantity of 250 litres is now sufficient to fill these, instead of the 600 litres of water previously required. As the water is renewed every three hours, Kramer is making considerable savings in terms of water usage: over 1.6 million litres per year, to be precise. The efficient design of the installation makes the conveyor belt of the ILV that bit shorter than before, up to and including the last line freezer. This also reduces energy consumption. Muller explains: “Kramer now has greater capacity, which means that energy consumption will increase. However, if I divide consumption by the number of kilos of fish that is processed, I can only draw one conclusion: the new freezer installation is much more energy efficient.”
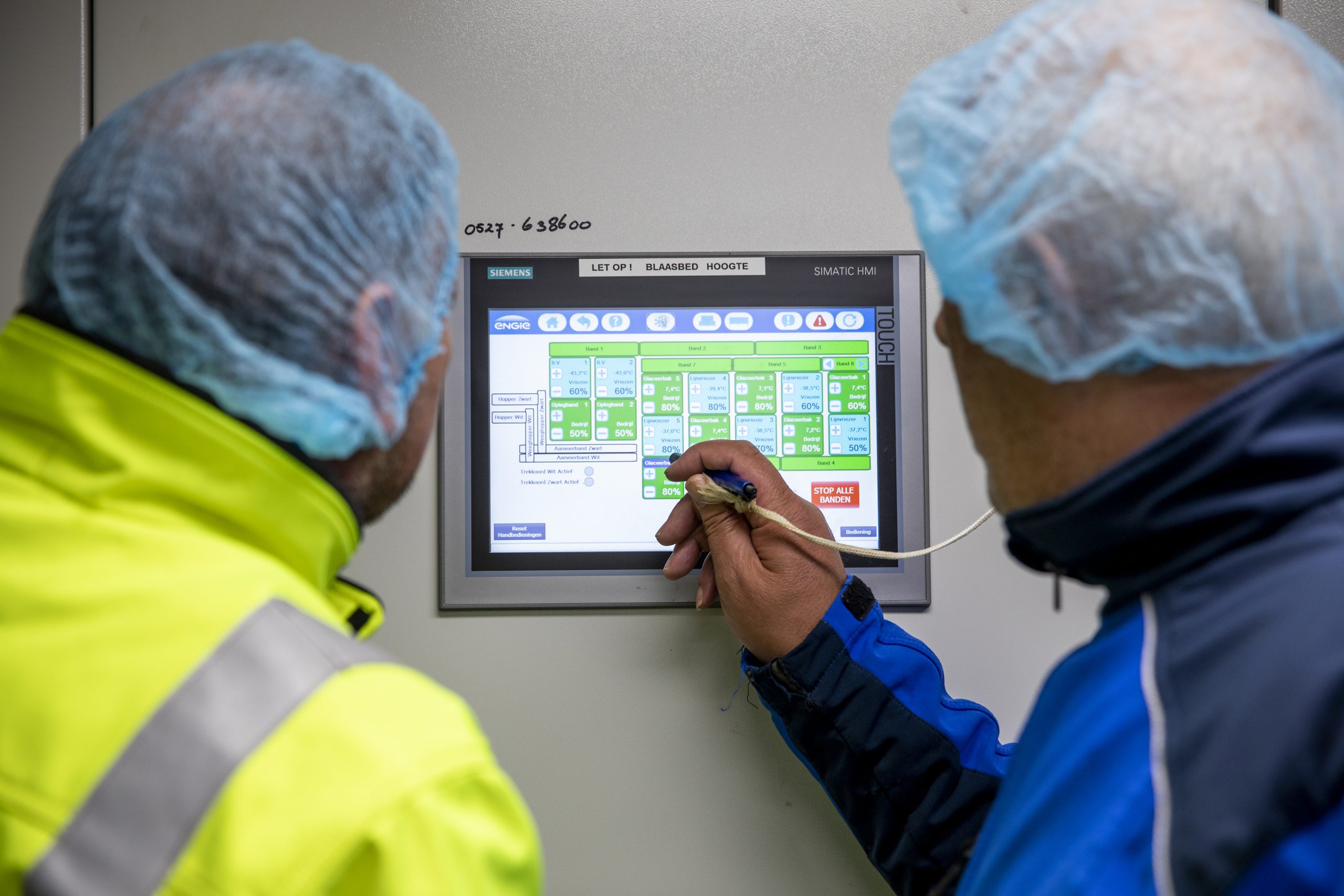
Although there are more line freezers and glazing containers, it is still much more convenient for the deep-freeze specialist. Sensors in the deep-freeze tunnels constantly check the temperature. What is more, the complete deep-freeze line is incorporated into the central operating system.
Romkes explains: “Whilst I previously had to input the settings manually for each tunnel, I can now operate all installations via a touchscreen: from the speed of the conveyor belts to filling of glazing containers. Cleaning has also become much easier, as we are able to open the hatches on the sides of the tunnels. Equans has taken this into consideration in its design.”
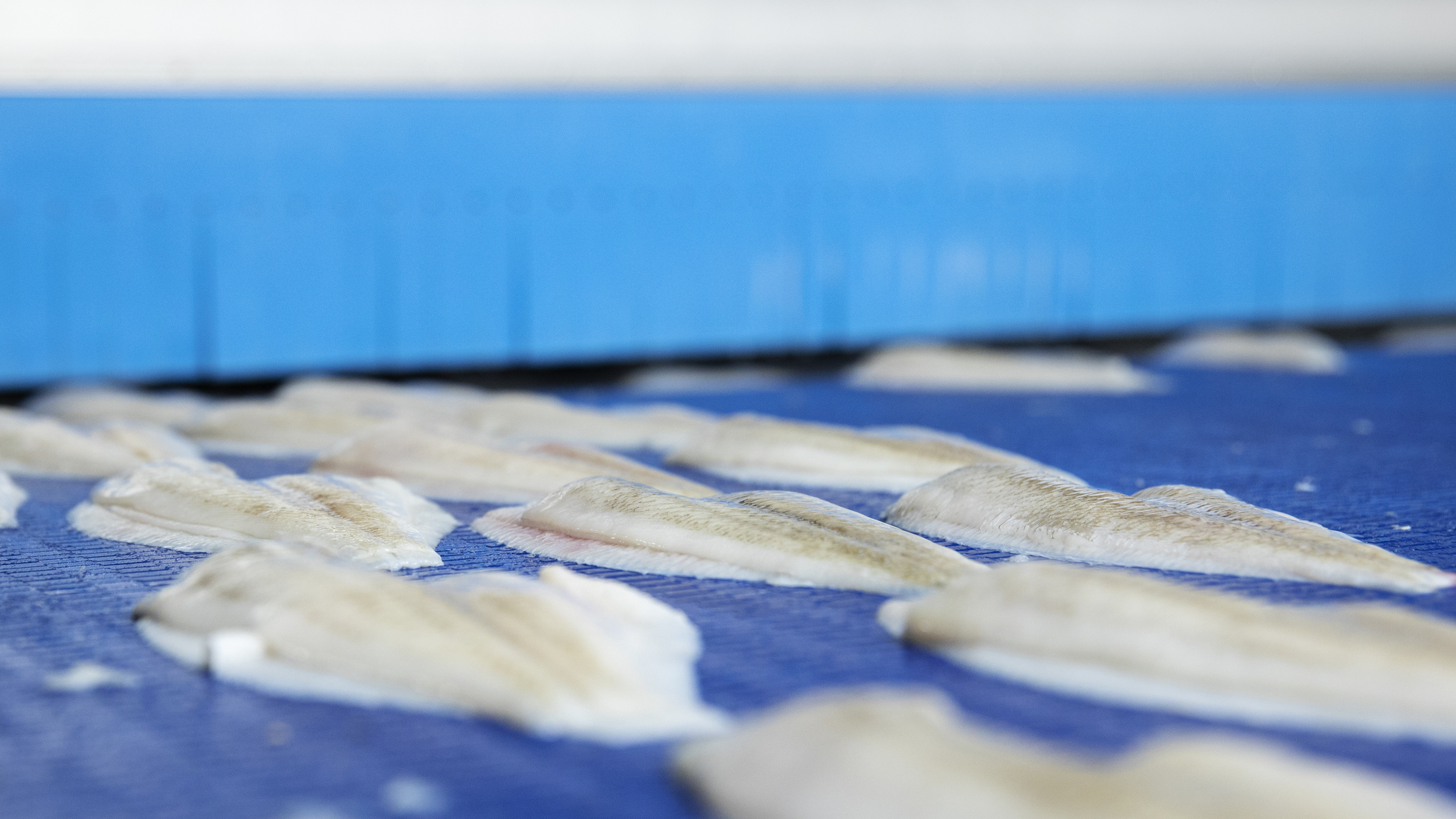
“Equans performed amazingly”, concluded Kramer. “The job needed to be completed within six weeks; after all the freezer is the heart of our company. If we don’t have that, then we are really stuck. But the installation was back in operation before the deadline. And as is fitting of a family company, Klaas and I are now preparing our sons to take over the company one day. In any case, the next generation will be able to use this freezer installation for years to come.”