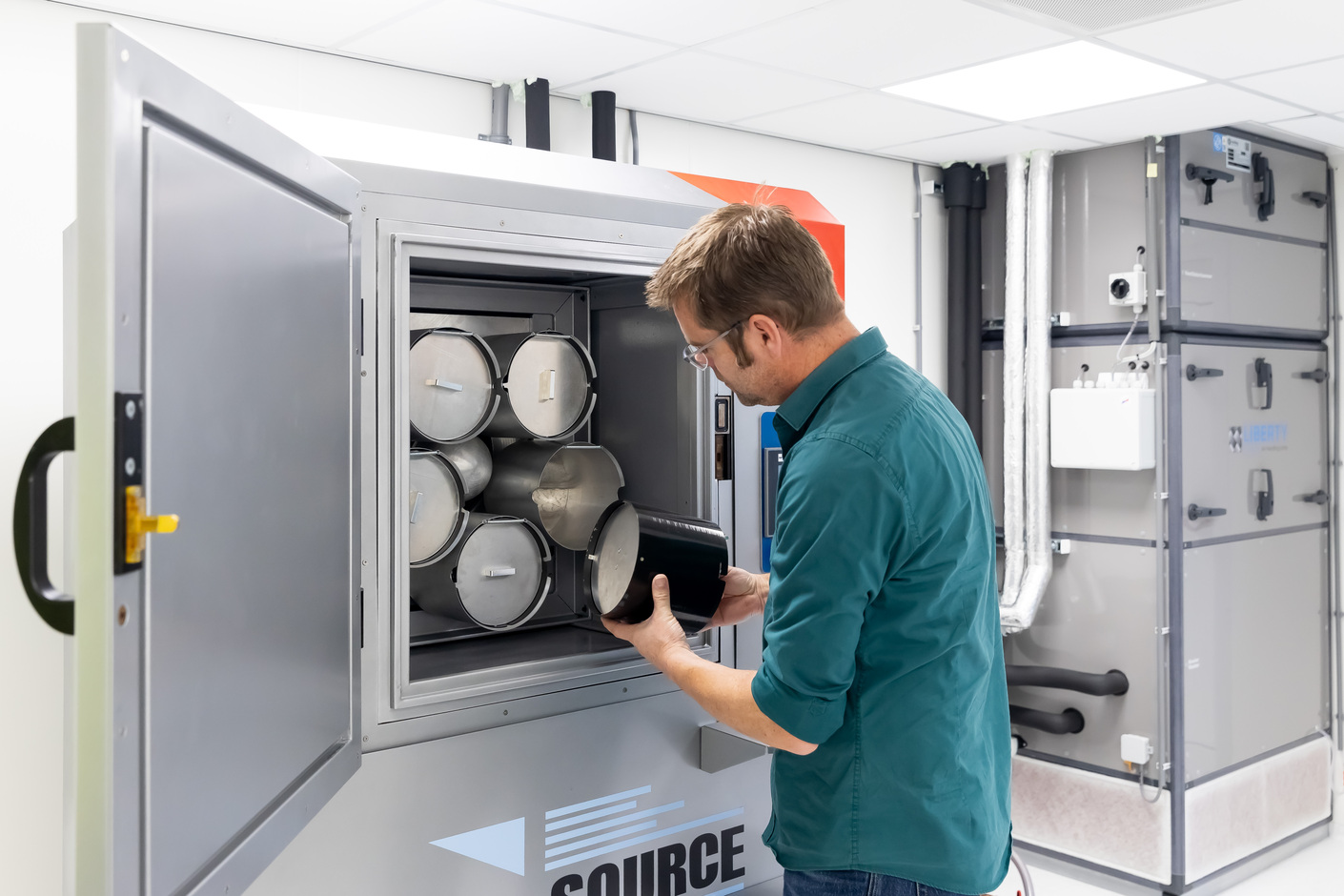
Wild onion flies, which occur naturally along ditches and roadsides near onion crops, lay their eggs in onion fields. Once a larva hatches, the insect feeds on the onion plant, causing damage to the crop. As the use of chemical pesticides is increasingly restricted, the demand for Sterile Insect Technique (SIT), as the biological pest control is known, is growing. This involves releasing sterilised onion flies into onion fields. When a sterilised fly mate with a wild fly, the egg remains unfertilised and does not hatch into a larva that eats the onion plant. By reducing the population of wild onion flies, onion crops are better protected.
De Groene Vlieg is the only commercial company in the world that produces sterilised onion flies. To meet the growing demand for SIT, the company opened a new nursery in Dronten. As an external project manager, Gert-Jan Meijlink outlined the design and requirements for the air treatment system, and started looking for a supplier.
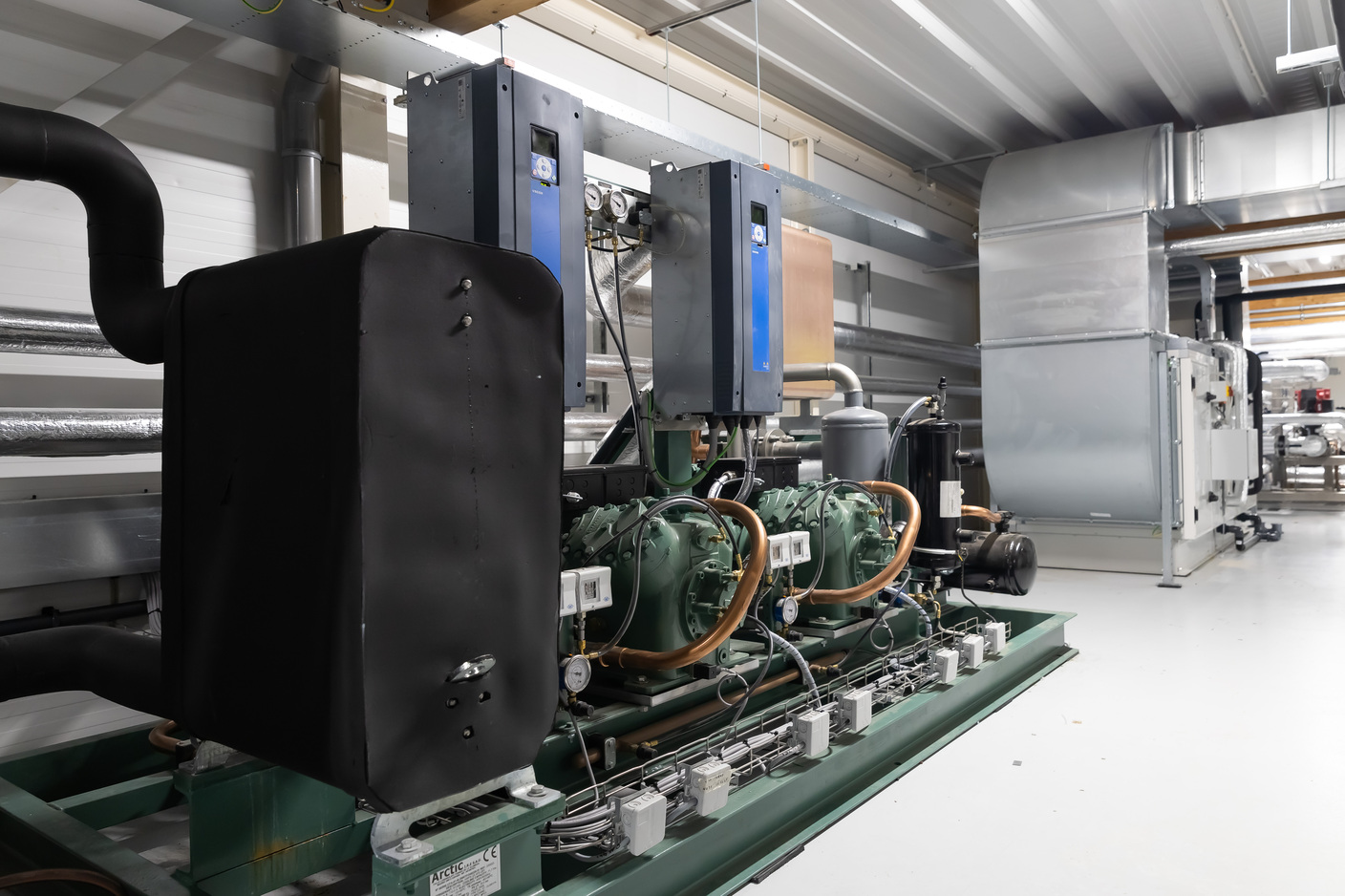
“Breeding of onion flies places incredible demands on the climate and air conditions. These must be properly regulated and monitored to prevent the flies from becoming susceptible to diseases”, says Meijlink. “We put our question to several parties. Equans came out on top with a drying system that offers what the critters need at every stage of their development. Because of an energy shortage and grid congestion in this polder, energy efficiency was an additional requirement. It was quite a puzzle. We managed to receive a second connection at the hall’s second house number. Although this was just sufficient for us, it becomes vulnerable when we are running at full capacity. Fortunately, Equans came up with energy-saving and heat integration solutions.”
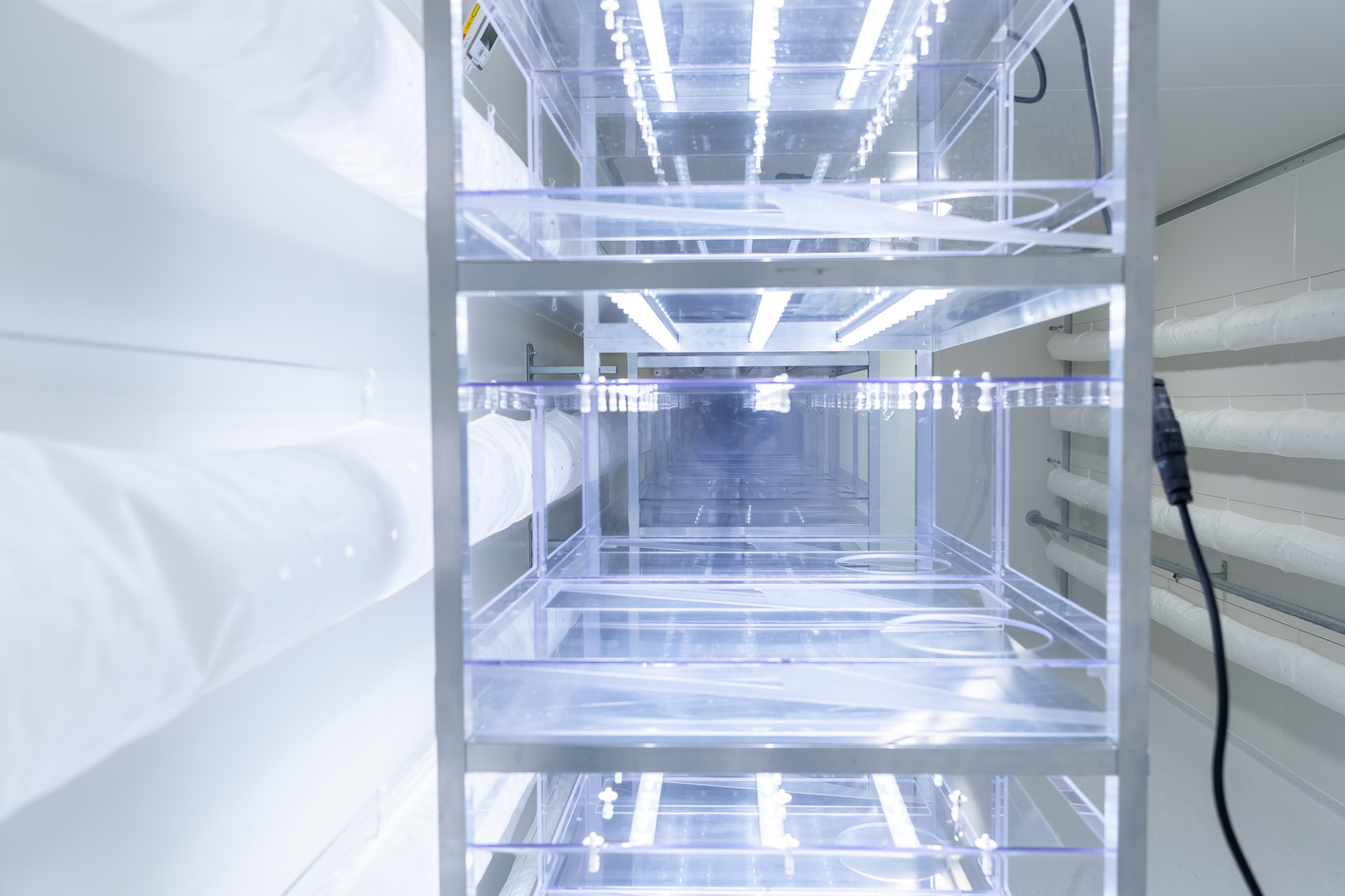
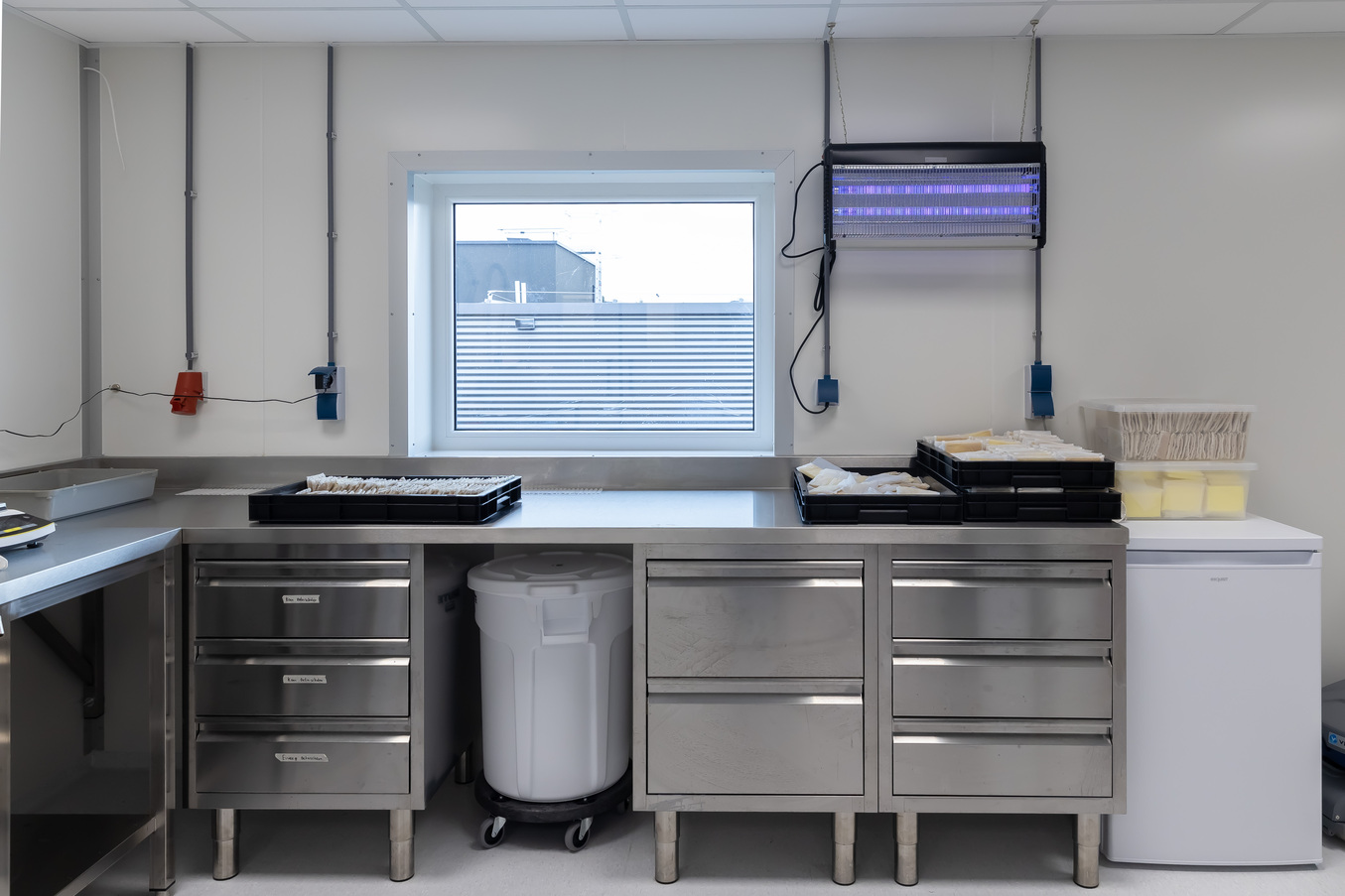
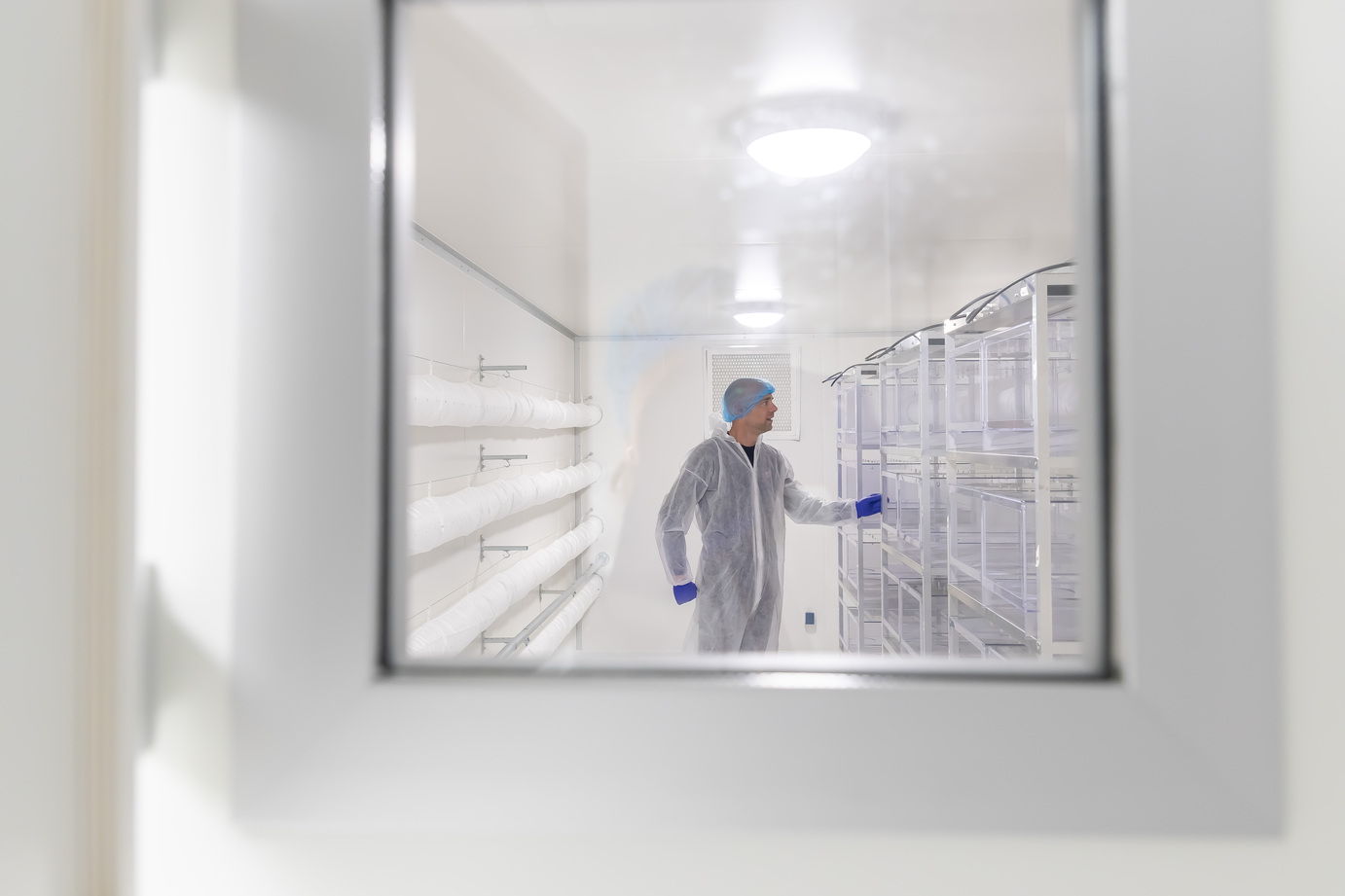
The Equans balanced air treatment system provides optimal conditions for each of the 3 phases of breeding. Meijlink explains that the first phase is egg production in 10 laying cells. “Such a cell is full of plexiglass cages with LED lights and wild onion flies. After mating, the females lay their eggs on a sponge that smells like onions. After 3 weeks, the eggs are harvested. The cell is then emptied, cleaned and prepared for the next egg-laying phase.”
As onion flies are very susceptible to pathogenic bacteria and spores, Equans designed an ingenious ventilation system. Paul de Kort of Equans explains: “A HEPA filter removes bacteria and spores from the incoming outside air. Air handling units filter the air (with a pre-filter and a HEPA filter), channel it to the desired air condition and circulate it through the cells. In the event of unexpected contamination, e.g. on staff clothing, we shut off the air supply in the contaminated cell and place it under negative pressure. Surrounding cells are deliberately kept at positive pressure. In this way, no germs can get into them, so production in those cells is assured. After changing the filters and cleaning the contaminated cell and the air handling unit, the egg cell is ready for use again.”
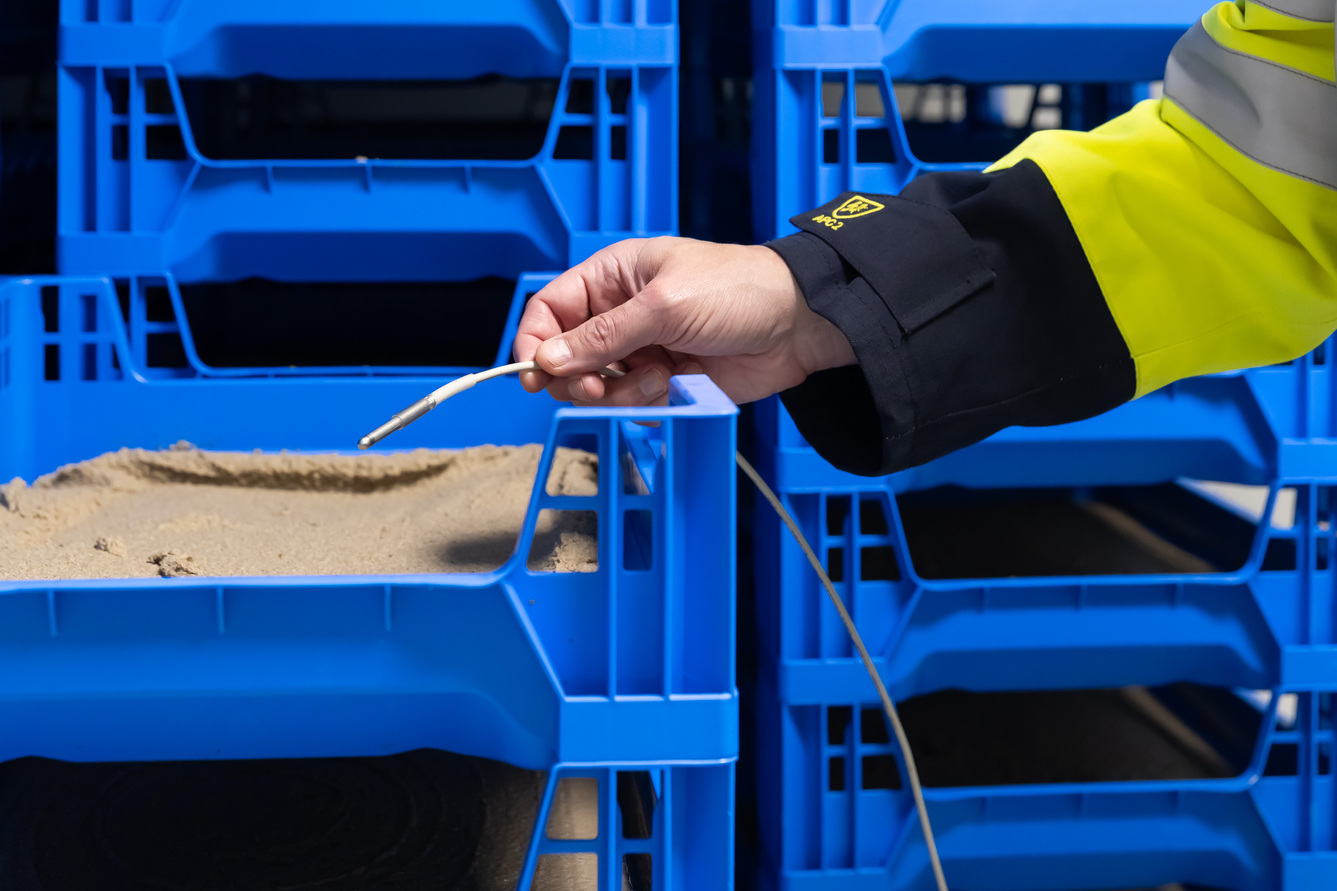
The development from larva to pupa is the second stage of the breeding process. For the eggs to last longer, they are dried in a drying cell for 2 hours. The dried eggs are then scattered in a breeding box and placed in the cell. Within a few days, the eggs turn into larvae that feed on the growth medium. According to Meijlink, air treatment is also crucial at this stage. “Hundreds of breeding trays are stacked in each 9-metre deep culture cell. With laminar airflow and temperature sensors, we can control the temperature of the larvae. This is important because although the larvae need heat to develop, they also produce heat when they move. By cooling them, we prevent them from getting too hot and the larvae from growing into pupae or even flies.”
After 3 weeks, it is time to remove the larvae from the trays. The mixture of larvae, residual feed, and faeces is combined with water, then aerated and strained. Carbon filters in the air handling unit remove as much of the ammonia smell from the faeces as possible. The larvae then move to a warmer pupation area in a container of vermiculite, a type of dried clay that absorbs moisture. Once they have developed into pupae after two days, they are cooled down to 2 degrees to stop the growth process. “In this way, we simulate the winter process of the wild onion fly”, says Meijlink. “The pupae only come out of the cold when needed, between April and September, when the onions are sown or planted.”
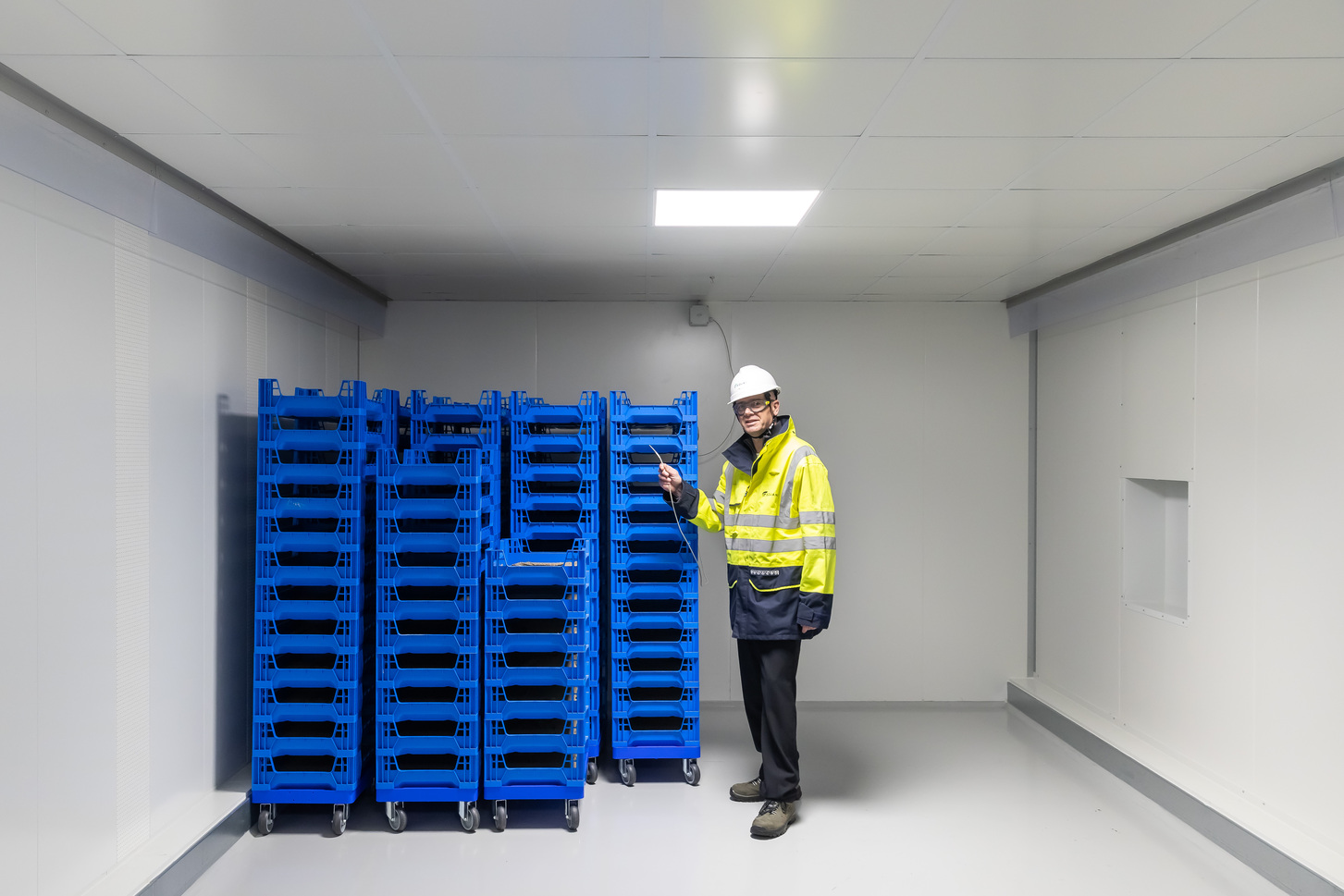
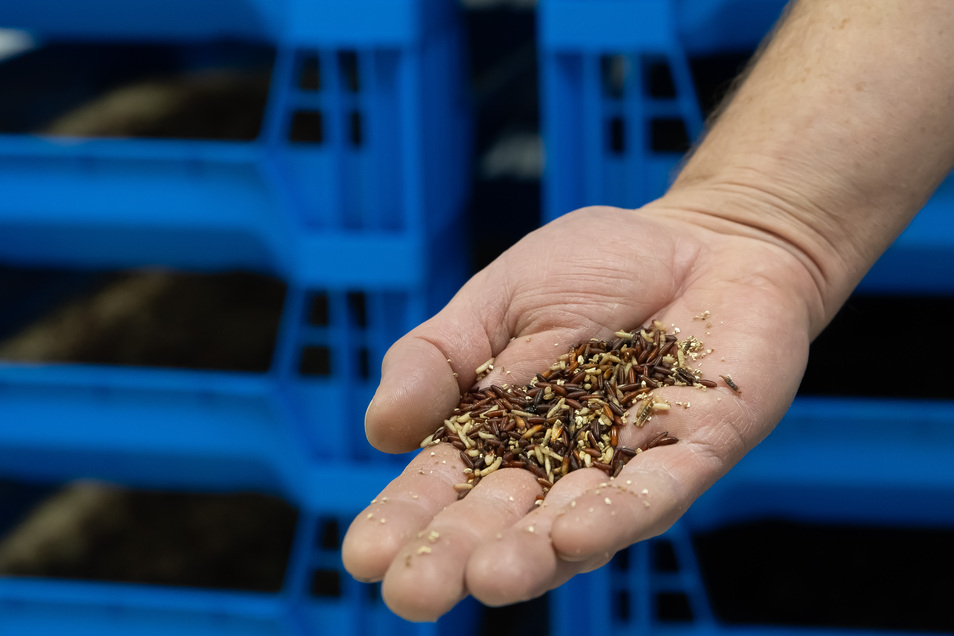
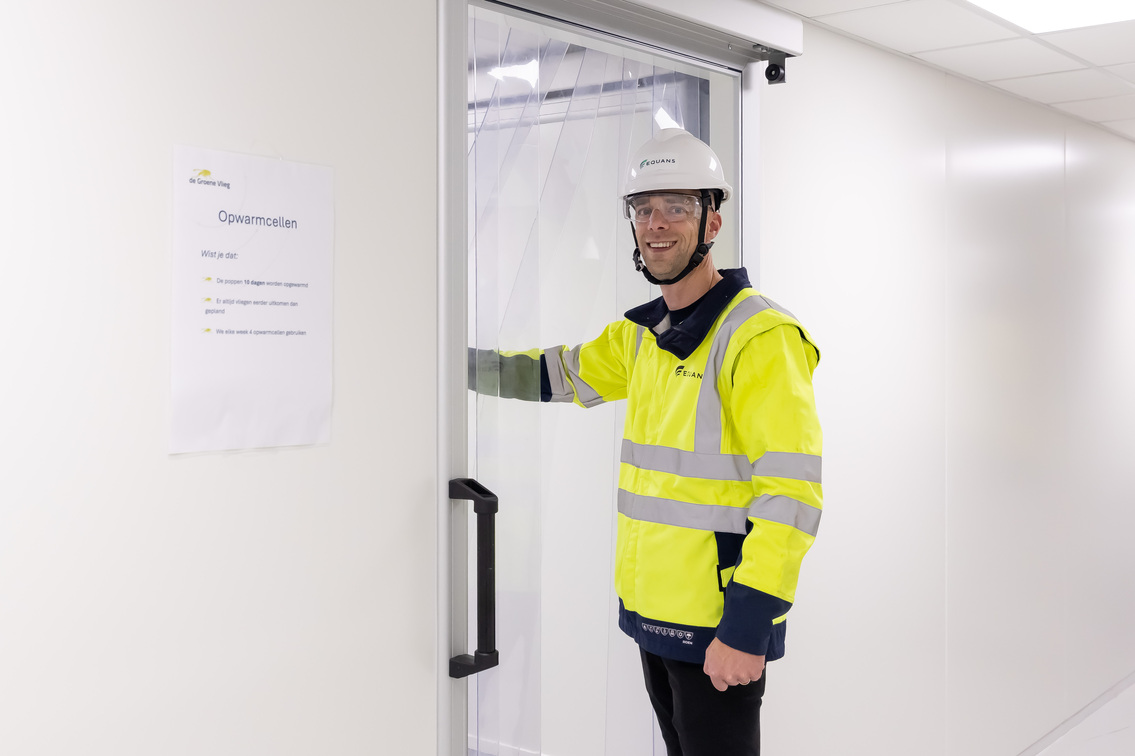
The third breeding stage is about making the sterilised onion fly. As soon as onion growers have filled their fields with onion plants, the pupae are transferred from the chilling room to the warming room for further development. On the 10th day, the day they develop genitalia, they receive a tiny amount of gamma radiation that destroys their reproductive organ. The irradiated, sterile flies are dyed pink and moved to the pupation rooms. These rooms are warmer, which tricks the pupae into thinking it is spring, and they hatch. When the sterilised onion flies come up to the light of a lamp, a cold blast of air underneath them puts them into a comatose state. This offers De Groene Vlieg the opportunity to catch the flies and release them along the edges of an onion field.
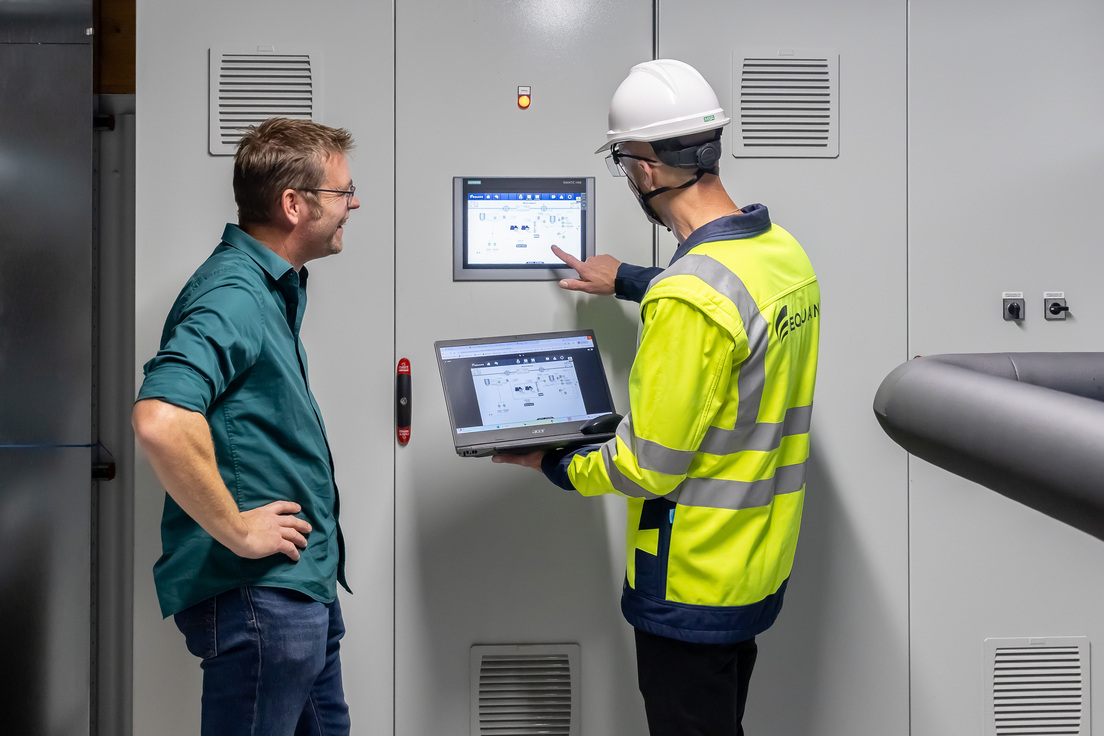
“With the new nursery, the potential production of sterile onion flies has doubled to 2 billion, maybe more”, says Meijlink. “Since it was commissioned in July 2024, we have seen significant improvements in the breeding process compared to the old nursery. These improvements were achieved even though the plant was built on many assumptions.” There was no data on the heat development of the animals in all breeding stages, nor was there any data on the heat output of the LED lamps. As a result, the company only uses part of its breeding capacity. “With the resulting data, in cooperation with Equans, we can adjust and optimise everything before we use the full capacity in the new year.”
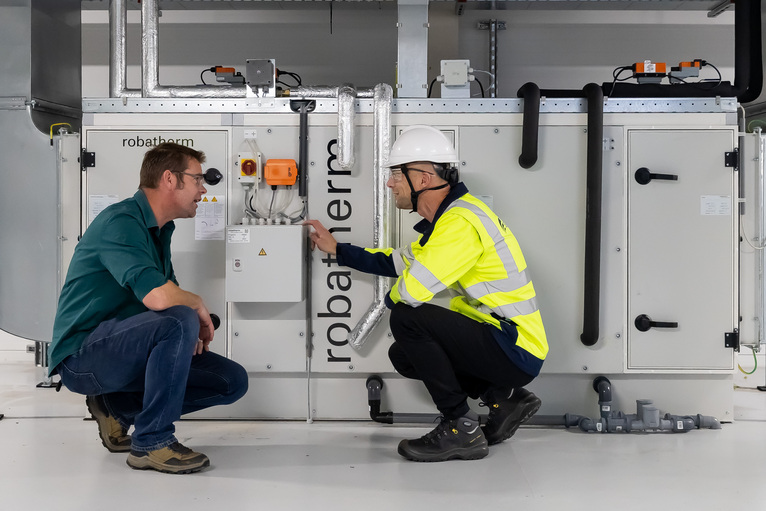
Working together to achieve process improvements is characteristic of Equans, according to Meijlink. “Both before and during the project, Equans’ project managers and engineers are open to discussions and adjustments where necessary. This works very well. I was looking for a party with whom I could work together to achieve the best design. I found that in Equans.”
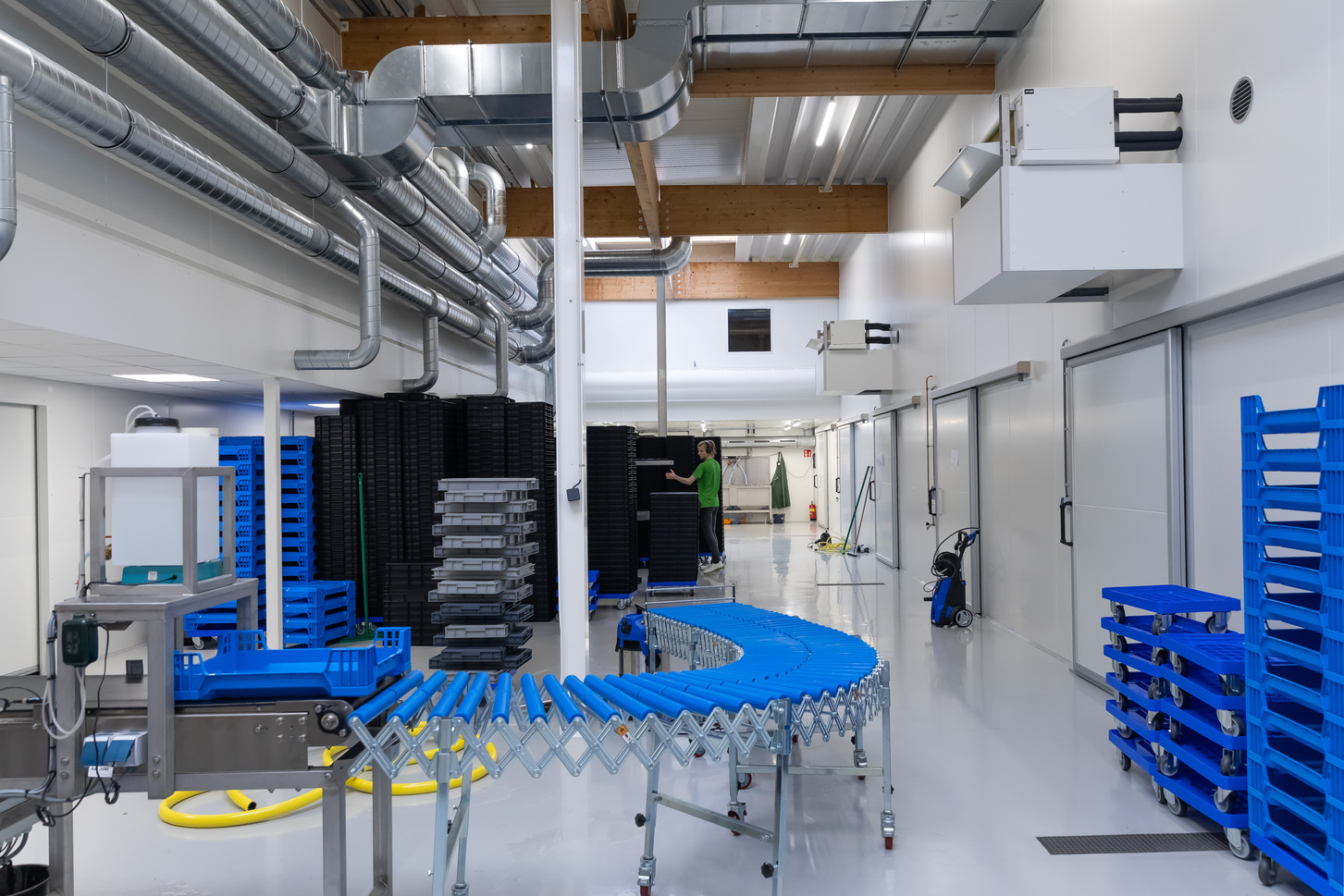
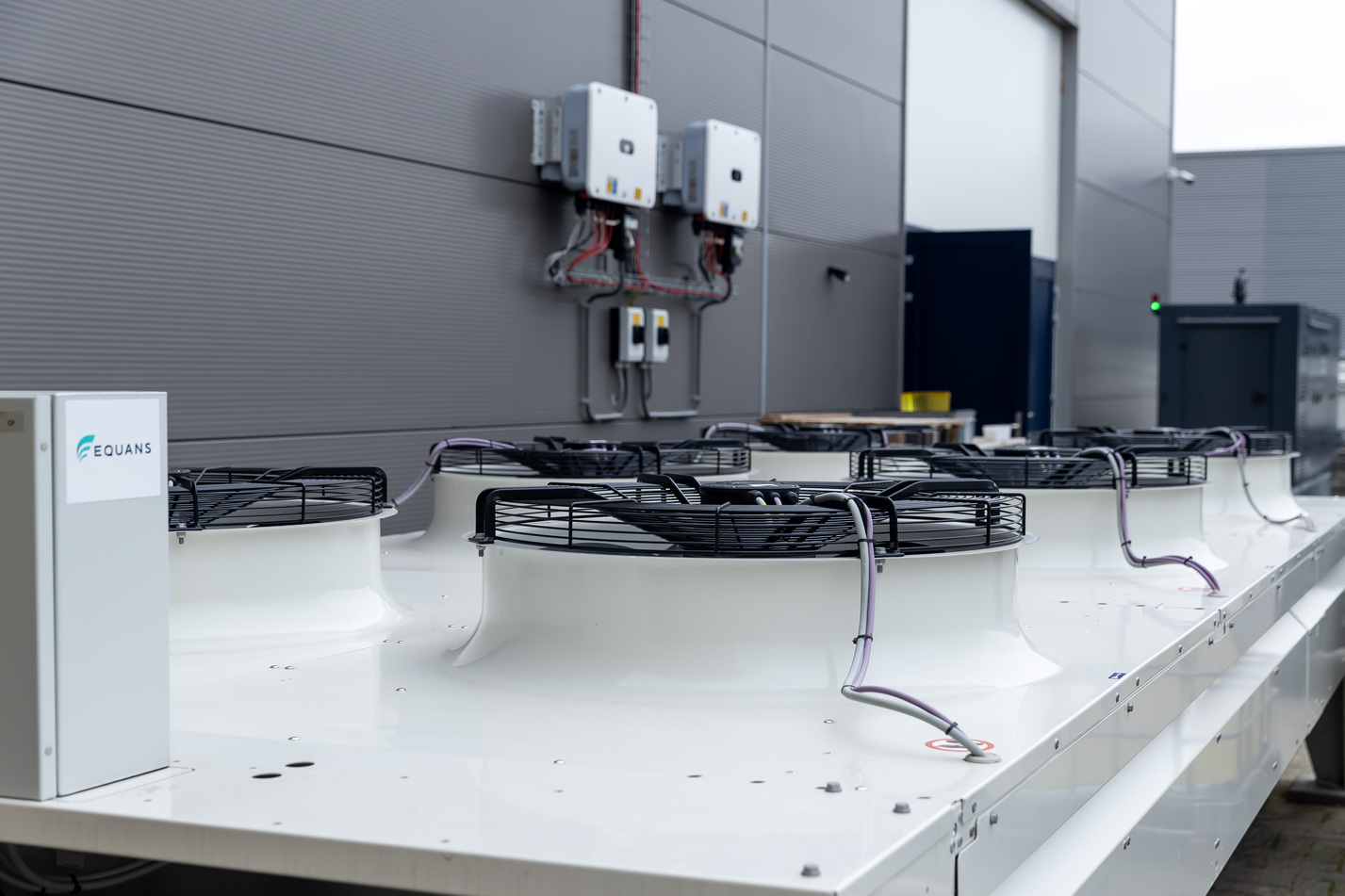
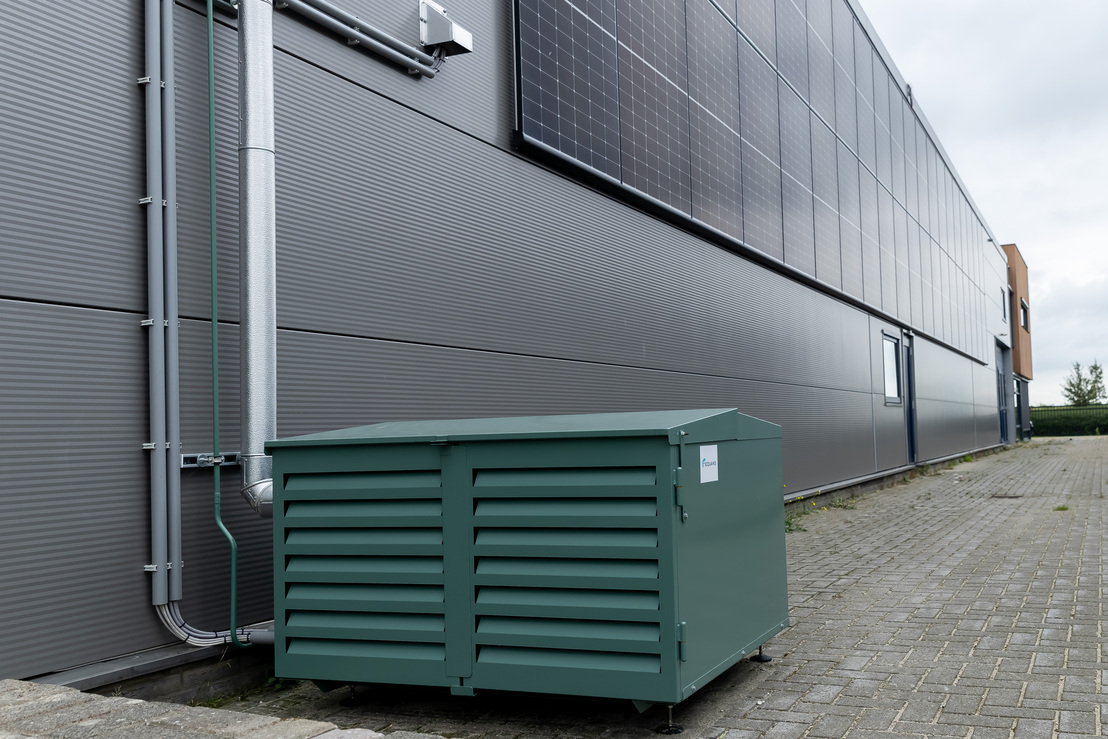
Equans Reference De Groene Vlieg
"*" indicates required fields